 |
Newsletter February 2015
|
|
 |
|
Organic Land Care Put into Practice A Blog Series by Peter Moon
In mid-December, O2Compost and Compostwerks (our Northeast affiliate) conducted a two-day workshop on Aerated Static Pile (ASP) Composting and Organic Land Care (OLC) Practices. I spoke on the subject of composting and Peter Schmidt discussed principles of OLC and how to convert a conventional garden to an organic garden. (Refer to our January Newsletter for details).
As I was listening to Peter during the workshop, I realized that my own lawn was in dire need of "conversion", so I have taken it upon myself to become a student of OLC practices. This series of articles will take us through next winter - and where it will go, I'm not altogether sure. I will be reporting in (nearly) real time what I do to my lawn and the results that I see.
The story begins about this time last year when my wife and I hired a landscaping crew to take care of our one acre garden.
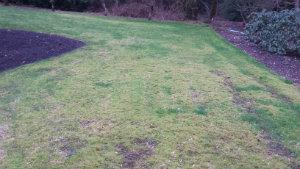 |
For the most part they have done a good job, but one day last spring I noticed that my lawn had what appeared to be "mange".
As it turns out, they had applied either a chemical fertilizer or an herbicide that destroyed 75% of my lawn and, no matter what we did the remainder of the summer, it stayed UGLY.
|
The few dark green areas that you see in the first picture are what is left of the grass. The yellow-green areas are pure moss, and the bare patches are simply that ... bare patches.
Destroying the lawn also revealed that there were many areas that had settled into a hummocky surface. Some of these depressions were due to mole activity and others resulted from erosion.
|
Today: As of this writing, I am in the process of importing coarse washed sand to fill in the low spots. When I've filled all of the holes, I plan to bring in high-quality compost and rake it into the sand to a depth of three inches. In early March, I will spread new lawn seed in these areas and rely on the spring rain to keep the soil wet.
|
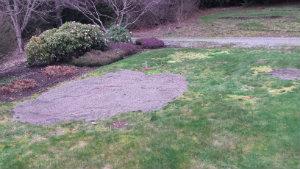 |
To better understand what is going on with my soil, I have taken a soil sample from a depth of 3-4 inches, and later today I will be sending it to a microbiological laboratory for testing. I will forward the lab test results to my friends at Compostwerks and follow their recommendations for applying organic fertilizers, soil amendments, and compost tea throughout the growing season.
I will let you know what happens in next month's O2Compost Newsletter.
|
Compost Business Success Story
Written by Peter Spalding (Owner of Fern Hill Compost in New York)
Fern Hill Compost started as the manure management system for Fern Hill Farm, an operation that bred Thoroughbred horses for the race track. After consulting with O2Compost, the composting facility was constructed adjacent to the farm's horse barn in the summer of 2009. The facility was designed with excess capacity for the collection of stall cleanings from other small horse-keeping operations in the area. Fern Hill Compost then established a container service utilizing one-cubic yard polyethylene containers which were collected weekly from a limited number of clients.
|
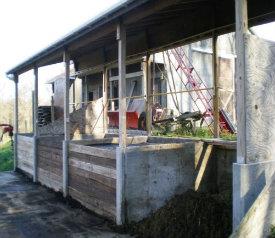 |
The composter was built with three aeration bins, plus one bin for collecting and mixing the raw feedstock. When there is sufficient material in the collection bin to build a batch, it is adjusted for moisture, mixed utilizing a bucket loader, and placed in the adjacent bin. Each composting bin has a water addition system with a set of fine spray nozzles to adjust moisture level in the material. A compost fabric cover is placed over each pile for moisture retention and insulating value.
Every 7-10 days during the active phase of composting, the material is removed, remixed, adjusted for moisture if necessary, and placed in the next bin where thermophilic temperatures for active composting are once again maintained. This process is repeated successively through the three aerated bins, then moved out for a curing period; historically in the yard but under compost fabric to shed water. Each handling process homogenizes the compost and breaks up clumps.
|
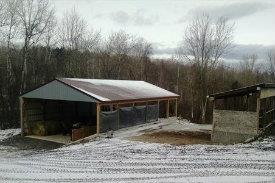 |
As a result, the finished product has a consistent granularity with no need for screening.
Recent improvements have included an extended concrete pad on the low side of the composter, and a 1500 square foot building on a concrete pad four feet below the grade of the extended working pad. This allows post stage one material to be bucketed through the open wall of the building for curing in a first-in/first-out method. The building space will also be used for bagging, palletizing, and finished goods storage.
|
Fern Hill Compost promotes the value of compost as a soil amendment through its website marketing and customer education.
Its marketing not only promotes the benefits of compost, but effectively focuses on the Fern Hill Compost product and what sets its quality part form other composts.
|
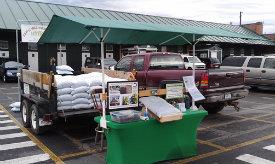 |
Although the container service was halted, compost production from our own herd of seven horses is sufficient to satisfy the needs of several garden centers with pallets of one cubic foot bags. Prior to that, I also sold retail at both the Syracuse and Rochester Regional Farmer's Markets, which provided an excellent opportunity to talk to people and educate them on the benefits of compost. Over the last four years, Fern Hill Compost has established an excellent reputation for a high quality product.
To learn more about Fern Hill Compost, visit www.fernhillcompost.com.
|
Peter's Rules of Composting - A 12-Part Series
Rule 10: Every System Has Constraints
Every manufacturing process involves raw materials, facilities equipment, trained personnel, and a distribution network. Every manufacturing process also involves systems to make all of these components come together in a timely and cost effective manner. Within every manufacturing process, there are constraints - some that are quite obvious and others that are not so obvious.
Composting is a manufacturing process where organic "waste" (our natural resource) are converted into a value added product (compost); and Rule 10 clearly applies.
Let's use a green waste compost facility as an example. With green waste (also referred to as yard debris) some of the materials tend to be coarse and woody and need to be reduced in size before going into the compost system. A grinder can be used for this purpose, but if the grinder is too small or it tends to break down a lot, this one piece of equipment will slow the process down and keep it from running smoothly. Unprocessed materials will accumulate upstream from the grinder and equipment downstream will operate well below their efficient processing rates, typically considered to be 80% of maximum.
If the grinder is replaced with one that works well and optimizes throughout, then some other constraint will appear - perhaps the screen that is used to refine the finished product now shows up as the new bottleneck in the system. Less obvious constraints can also appear:
- Facility owners and site personnel lack proper training;
- The types and volumes of materials being accepted at the site require operating permits;
- A lack of good housekeeping results in odors and neighbor complaints;
- Little attention is paid to the marketing of compost products, etc.
In Rule 8 (December Newsletter), I recommend starting small and scaling up in planned increments. In the planning process, it is important to look at all aspects of the compost system to anticipate the constraints that will inevitably show up. A flow-diagram is a great tool that will assist in this evaluation process.
The First Corollary to Rule 10: "Buy a tractor or front-end loader that is one size larger than what you think you will need."
Reference: The Goal: A Process of On-Going Improvement by Eliyahu M. Goldratt, 1992 This book was written as a novel, and as a novel it's OK but not great. However, the message it delivers is excellent and one that should be considered by everyone who is related to a manufacturing process.
Previous Rules:
Rule 1 - Start With the End in Mind (April Newsletter) Rule 2 - To Learn to Compost, One Must Compost (June Newsletter) Rule 3 - Every Question About Composting Has Only One Answer (July Newsletter) Rule 4 - Oxygen is the Secret to Composting (August Newsletter) Rule 5 - Water is the Highway of Life (September Newsletter) Rule 6 - Composting Takes Time (October Newsletter) Rule 7 - There are No Decimal Points in Composting (November Newsletter) Rule 8 - Think BIG - Start Small (December Newsletter) Rule 9 - It's Important Critical to Make Mistakes (January Newsletter)
|
A New Compost System Comes On-Line |
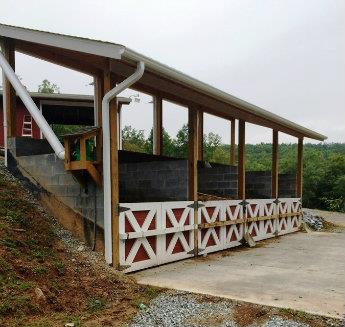
|
OWNER: Marcia S.
LOCATION: Tryon, North Carolina
Nine horses
The finished compost is spread back onto the pastures and shared with neighbors and friends.
This system can also be found on our website (Sharpe Farms).
|
Coming Events
March 15 - 18, 2015 International Conference on Solid Waste and Management - Philadelphia, Pennsylvania Peter Moon will be speaking about the onsite compost system that we designed for the city's women's prison and its recent expansion to accommodate food waste generated by 2500 prisoners. For more information, visit solid-waste.org/2015-conference-2/
April 29 - May 2, 2015 ASP Hands-On Workshop - Seattle, Washington This 3-day event bridges the gap between the classroom and the field. We are now taking registrations. Email: sherri@o2compost.com Space is limited. Early registration is advised. View our event Flyer for details.
|
|
Protecting Our Land, Air and Water Resources
|
O2Compost Price-Moon Enterprises, Inc. PO Box 1026 Snohomish, WA 98291
|
Phone: 360-568-8085 Email: info@o2compost.com
www.o2compost.com
|

|
|